Cleaning Up a 1947 Marlin® 39A
by Roy Seifert
Click here to purchase a
CD with this and all Kitchen Table Gunsmith Articles.
Disclaimer:
This article is for entertainment only and is not to
be used in lieu of a qualified gunsmith.
Please defer all firearms work to a qualified
gunsmith. Any loads
mentioned in this article are my loads for my guns and have
been carefully worked up using established guidelines and
special tools. The
author assumes no responsibility or liability for use of
these loads, or use or misuse of this article.
Please note that I am not a professional gunsmith,
just a shooting enthusiast and hobbyist, as well as a
tinkerer. This
article explains work that I performed to my guns without
the assistance of a qualified gunsmith.
Some procedures described in this article require
special tools and cannot/should not be performed without
them.
Warning:
Disassembling and tinkering with your firearm may
void the warranty. I
claim no responsibility for use or misuse of this article.
Again, this article is for entertainment purposes
only!
Tools
and firearms are the trademark/service mark or registered trademark
of their respective manufacturers.
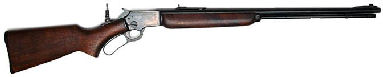
Introduction
Ever since I can remember I have been fascinated with
firearms. Unfortunately,
since my parents were not outdoors people nor sportsmen, my
exposure to shooting was limited to the high school rifle
team. On my 21st
birthday I purchased a .357 magnum revolver which began my
journey into the world of shooting and firearms.
One
of the guns I’ve always wanted to have was the Marlin®
39A lever-action .22 rifle.
Believe it or not, this desire began with an arcade
game. As a
teenager I used to play a shooting gallery arcade game that
simulated shooting bottles with a lever-action rifle.
I always thought that would be fun to do in real life
so I started researching lever-action rifles.
At the time I did my initial research, lever-action
rifles mostly came in .30-30 or .22 calibers.
The .30-30 was primarily used for hunting and would be
too expensive for plinking (I wasn’t reloading at the time)
so I concentrated on .22’s.
The one that kept coming up was the Marlin® model 39A.
The
Marlin® 39A has been in continuous production longer than any
other rifle in
America
, beginning in 1891. Annie
Oakley used one for her exhibition shooting.
Rather than being made of aluminum and plastic, this
rifle is all blued steel and American black walnut.
Its 24-inch barrel and full length magazine tube allows
me to load 26 short, 21 long or 19 long rifle cartridges.
Plus, I’ve always thought the takedown capability was
very convenient, and also pretty cool.
This rifle was always more expensive than other .22s on
the market, so over the years I’ve made do without a 39A.
Recently
on Gunbroker.com I
found a used, Marlin® 39A for $380; about twice the price for
a new Brooklyn-made lever-action .22.
Prices for new and used 39A’s were running $475+ so I
felt this was a good deal.
However, the fact that this rifle was built in 1947 (as
indicated by the prefix letter D in the serial number), it did
not have a hammer-block safety, and it came with a tang peep
sight made this an outstanding
deal in my estimation!
Initial
Assessment
This rifle appeared to be in great shape.
There were some dings in the butt stock and forearm but
these could be steamed out.
The metal and bluing were in excellent condition with
just a bit of surface rust and a few dings and scratches,
typical of a 60+ year old rifle.
It was also very dusty indicating that it had been
sitting around for some time.
There’s really no way of telling how many rounds have
been fired through this rifle, but the action was glass
smooth, and after a thorough cleaning, the bore looked bright,
and the rifling sharp. This
was not the light, aluminum and plastic lever-action .22 I was
used to. Instead,
this rifle felt heavy and solid; just like my other big-bore
Marlin® lever rifles.
Magazine
Tube
As with any used gun that I purchase, I completely
disassembled the rifle to give it a thorough cleaning and
inspection. The
first problem I found was with the inner magazine tube
assembly. It had a
slight bend about six inches up from the follower, and the
retaining pin that held the knurled plug in the tube was too
loose. This inner
magazine tube assembly was made out of aluminum, not brass,
and there were grinding marks on the tube where the retaining
pin holes were drilled which made me think it was a
replacement. Research
on the Internet indicated that this year gun came with an
aluminum inner magazine tube, so the replacement was period
correct.
I
disassembled the inner magazine tube and inserted a wooden
dowel so I wouldn’t over-bend the tube.
I gently applied pressure on the bend which was easy to
see because it was rubbed shiny.
I was able to get the tube fairly straight so it slid
easily into the outer tube.
I’m wondering if this was done on purpose to prevent
the tube from falling out, or sliding back in when loading
cartridges into the outer tube.
I took a cleaning rod with a .45 caliber cleaning patch
and thoroughly cleaned the inside.
It took about 6 patches to clean 60+ years of gunk,
then I ran a lubricating patch through the tube.
I
reassembled the inner magazine tube and tried to replace the
solid retaining pin with a roll pin but the hole was too
large. A larger
roll pin would not fit in the notch in the outer magazine
tube, so I installed the retaining pin and staked it in place
with a prick punch. To
finish my fix I put a 5/16” O-ring in front of the knurled
plug, which provided just enough tension to prevent the inner
tube from falling out.
Re-Crown
the Muzzle
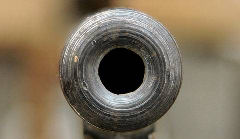
As
shown in the above photo, the muzzle crown was rough and
pretty dinged up. A
poor muzzle crown will affect accuracy. I
decided to re-crown the muzzle, not only to make it look
better, but to also allow for maximum accuracy.
A
professional gunsmith uses a lathe to cut a new crown, but I
don’t have a lathe. I
used a 79-degree crown cutter I purchased from Brownells to
cut the crown by hand. This
cutter makes a recessed target crown, but I used a 1/2-inch
diameter cutter – smaller than the diameter of the barrel
– so I wouldn’t cut out to the edge of the barrel.
I installed the .22 pilot, handle, and a 1/2-inch stop
collar onto the cutter. The
stop collar makes the cut smooth, rather than uneven with
chatter marks. In
the photo above the stop collar is set back to show the
cutting teeth. I
adjusted the collar so it was almost flush with the front of
the cutter.
I
lubricated the pilot and cutting teeth with cutting oil and
turned the cutter clockwise.
I turned the cutter only in one direction; otherwise I
could break the teeth. I
cleaned chips off of the cutter and muzzle and lubricated the
cutter frequently. I
cut until the stop collar touched the front of the barrel.
You can see the nice, clean muzzle in the above photo.
After
I cut the new muzzle crown I used a brass muzzle lap to
final-lap the muzzle. This
ensured the lands and grooves were nice and sharp at the
muzzle which results in improved accuracy.
I took the smallest brass muzzle lap and chucked it in
my hand drill. I
put some 400-grit lapping compound on the end of the lap, and
with the drill running at a medium speed, I pressed the round
end of the lap against the muzzle and used a rotating motion
with my wrist to ensure the muzzle was lapped evenly.
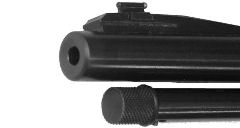
Cutting
the new crown left a sharp edge on the front of the muzzle.
I took a 400-grit stone and went over that edge just
enough to smooth it down.
Finally, I blued the exposed crown with cold blue to
prevent the metal from corroding.
I degreased the crown with acetone, plugged the bore,
then immersed the muzzle in Van’s
Instant Gun Blue for about 5 minutes.
I wiped off the excess bluing solution, then treated
the metal with gun oil to stop the bluing process.
The above photo shows the result.
Trigger
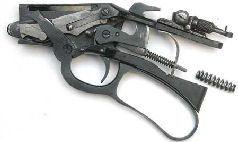
I
didn’t really measure the trigger pull before starting this
project, but I did want it lighter.
To reduce trigger pull first I replaced the hammer
spring. I removed
the original hammer spring by pushing the top of the
mainspring plate to the right until it slid out of the frame.
I installed a Wolff
reduced power hammer spring that I ordered from Brownells.
In the above photo you can see the original hammer
spring next to the installed Wolff spring.
To
further lighten the trigger pull I pulled up on the trigger
return spring until it made light contact on the trigger.
After reassembling the rifle the trigger measured 2 1/2
pounds, and the rifle was easier to lever.
I pulled the bullets and powder from various .22’s I
had to test if the lighter hammer spring would still pop a
primer. Of the
three different types of .22’s I tested, the rifle fired the
priming compound with no problems.
If you notice in the above photo there are two notches
in the bottom of the receiver for the mainspring plate.
If the replacement hammer spring was not strong enough
I could have used the forward notch thereby increasing spring
tension.
Rear
Sight
This rifle came with a fixed, non-folding, rear sight.
I removed the rear leaf sight by drifting it out of the
dovetail from left to right.
I don’t really need two sights installed, and the
leaf sight got in the way of the peep sight.
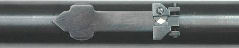
I
ordered a Marble Arms®
replacement folding rear sight from Brownells #579-000-082 and
installed it from right to left in the existing dovetail.
This sight does not use an elevator to raise the sight;
rather there is a blade insert that slides up or down in a
channel and is locked in place with a screw.
The insert has a white diamond and has two different
notches, round and V; I used the V.
Plus, this sight is also windage adjustable.
Now I have the tang peep sight as my primary sight, and
the folding leaf sight as a backup.
I keep the leaf sight folded down when using the peep
sight.
Front
Sight
The front sight blade came with a brass bead, but as I get
older I have trouble seeing that little tiny bead, even after
polishing it up with a drop of Brasso®
on a cleaning patch. I
decided to replace the bead front sight with a post front
sight.
Brownells
sells a post front sight with a white line in the center for
$30. I decided to
try to fabricate my own using materials I had on hand.
Brownells sells a 12-inch piece of 3/8” dovetail
blank which used as the base for my new sight, and I had some
1/8-inch steel bar for the post.
I
used CorelDraw® to design the front post, then exported the
pattern to my CAD/CAM program.
I used my hobby CNC mill to cut a channel in the base
for the post, and to cut out the base from the dovetail blank.
I also used the CNC mill to cut out the post from the
1/8-inch bar stock. I
silver-soldered the post into the channel I milled in the
base, then milled a 3/64 groove in the front ramp of the post.
I bead-blasted the new sight, cold-blued it, then
applied white appliance touch-up paint to the groove.
Refer to my article Fabricating
a Custom Front Sight for details.
The
dovetail base was just slightly larger than the dovetail in
the barrel ramp. I
used my 65-degree dovetail file to file one side of the sight
base until it fit.
Ghost-Ring
Rear Sight
The fact that this rifle came with an original tang peep sight
was one of the selling features for me.
The tang peep sight had a single, target aperture that
folded forward out of the way so the peep could be used as a
ghost-ring. I find
that a ghost-ring works well for my aging eyes, and I don’t
have to worry about lining up a rear sight, front sight, and
target. My eye
doesn’t really see the large aperture ghost-ring, but my
brain does and automatically lines up the front sight into the
center of the ghost-ring, so once sighted-in, where ever the
top of the front sight is, that is where the shot will go.
However,
this sight was not windage adjustable.
When I attempted to bore-sight the rifle with a laser I
discovered I had to drift the front sight almost 1/8-inch to
the left, which meant I also had to drift the leaf sight that
much to the left as well.
This did not appeal to me and I felt it destroyed the
aesthetics of the rifle, so I decided to replace the tang peep
sight with a windage-adjustable ghost-ring.
I
found three different types of peep sights for the 39A that
were adjustable for both windage and elevation that I could
use as a ghost-ring; two were receiver mounted and one was
tang mounted. Those
three sights were:
- XS®
Sight Systems model ML00075– This is a
receiver-mounted ghost-ring that comes with a square post
front sight. Although
this sight is adjustable for both windage and elevation it
is more of a modern hunting sight and didn’t really
appeal to me.
- Williams®
Gun Sight Company Inc. models FP and 5D – These are
also receiver mounted sights adjustable for both windage
and elevation. The
5D is the less-expensive model and does not have the
locking micrometer adjustments of the FP.
To be used as a ghost-ring sight I would simply
unscrew the aperture and use the threaded hole.
- Marble
Arms® model 009827 – This is their tang peep sight
#8 and it is designed to fit the peep sight holes in the
tang of the older 39A models.
This was the most expensive of the three sights,
but was also more period-correct, and adjustable for both
windage and elevation.
I have this sight on a number of other lever rifles
I own and prefer it over other styles.
To make it a ghost-ring I unscrew the aperture and
use the threaded hole.
I
decided to replace the original 1947 peep sight with the
Marble Arms® #8 sight. The
sight base and screws fit the predrilled and tapped holes
perfectly. I was
able to adjust both windage and elevation so I didn’t have
to play with the front sight.
Refinishing
the Stock
This rifle came with a dark walnut butt stock and forearm with
an oil finish. However,
over the years the wood had acquired some nicks and felt dry
and rough to my hands. I
decided to refinish the wood to make it smoother and more
attractive. This
is not a collectable, it is a shooter, but I wanted it to look
good and function well.
I
removed the forearm by first driving out the magazine tube
band pin. I then
removed the two forearm tip screws and pulled the magazine
tube out of the rifle. The
forearm fell out in my hands.
I removed the butt stock by removing the tang screw and
pulling the butt stock off of the receiver.
One
of the goals of refinishing a gun stock is to remove as little
wood as possible. Over
the years I have ruined gun stocks by over-sanding trying to
remove old finish. The
secret is to use a good quality stripper so I don’t have to
excessively sand the wood.
I
stripped the old finish off the wood by applying BIX®
stripper that I purchased at my local home improvement store.
I applied the stripper with a brush by dabbing it on
very thick and letting it set for 15 minutes, then I scraped
off the excess stripper with a business card.
I applied a second coat of stripper and again let it
set for 15 minutes. I
again scraped off the excess stripper with a business card,
then scrubbed the wood with water and #2 steel wool as
described in the instructions.
After
stripping the wood I steamed out any dents by applying a wet
washcloth to the bare wood and ironing the wet cloth.
This also raised the grain in preparation for sanding.
Once
the wood was dry I sanded it with 400-grit sand paper.
I only wanted to remove the feathers raised from the
steaming process, not alter the shape of the wood.
I wrapped a strip of 400-grit paper around a roll of
soft leather. The
leather roll helps to maintain the shape of the wood without
leaving any dents or flat spots.
The above photo shows the difference between the
original butt stock and the stripped and sanded forearm.
I
removed the sanding dust with a tack rag (an old T-shirt
worked well) and applied a coat of Minwax®
Gunstock #231 stain. This
stain goes on brick red in color, but when the excess is wiped
off, it leaves a brownish-red color.
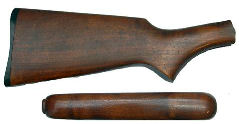

Over
the years I’ve tried different finishes on gunstocks.
Each has advantages and disadvantages; some are easier
to apply, whereas others are easier to repair.
My favorite is Birchwood
Casey Tru-Oil®. It
is easy to apply, gives a beautiful soft sheen luster to the
wood, it’s durable, and it’s easy to repair.
After the stain dried I applied three coats of Tru-Oil®.
I allowed each coat to dry for 12 hours, then went over
the wood with 000 steel wool.
The above photos show the refinished fore end next to
the original butt stock, but really don’t do justice to the
result.
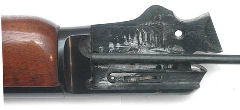
Before
reinstalling the outer magazine tube I ran a cleaning patch
through it to make sure it was cleaned and lubricated.
Very few people ever clean the magazine tube, which can
accumulate dirt. In
fact I once had a lever-action rifle stop feeding and jam on
me because the follower got jammed in a dirty magazine tube.
Wouldn’t you know it happened in the middle of a
shooting competition!
When
I tried to reinstall the outer magazine tube I soon discovered
just how difficult this was to accomplish.
Because I had to install the forearm first which
covered the magazine tube hole in the receiver, I couldn’t
get the tube aligned in the hole.
My solution was to install the outer magazine tube
until it touched the front of the receiver, then I took a
pistol/revolver cleaning rod and inserted it into the
cartridge feed hole in the receiver.
I used the cleaning rod to align the tube; it literally
took 5 seconds to wiggle (gunsmithing technical term J)
the rod while pressing on the magazine tube until it clicked
in place.
Butt
Plate
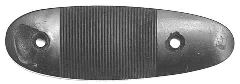
The
butt plate had a number of chips around the holes probably
because this was not an original butt plate and the
countersinks didn’t fit the screws.
There was a large chip missing from the top of the butt
plate as you can see in the above photo.
Since this butt plate fit the stock I really didn’t
want to purchase a new one and go through all the fitting, so
I decided to try to repair it with epoxy.
First
I took a countersink bit and trimmed around the holes.
This allowed the screws to fit better.
Then I sprayed some release agent I purchased from
Brownells around the top screw and mounted the pad to a piece
of 2x4. The
release agent prevented the epoxy from sticking to the screw.
I read somewhere that Pam®
cooking spray makes a good epoxy release agent, but I’ve
never tried this. I
did not tighten the screw because I wanted to be able to
rotate the butt plate.
I
drilled two small holes in the hollow I planned to fill with
epoxy. This gave
the epoxy some additional hold.
I mixed some J-B
Weld® and added some black dye from a Brownells Acraglas®
bedding kit, then applied the epoxy to the chipped area using
a toothpick. I
made sure the holes I drilled were filled with the epoxy, and
that the epoxy was higher than the surface of the butt plate.
In the above photo notice the cleaned up countersink
around the bottom hole. While
the epoxy was curing I rotated the butt plate to prevent the
top screw from getting glued in place.
After
the epoxy cured I used 180-grit sand paper wrapped around a
file and sanded it down flush with the surface of the butt
plate. Then I
polished the surface with 400, 600, then 1000-grit wet/dry
sand papers also wrapped around a file.
The file kept the sand paper flat and gave me more
control when sanding. Finally
I used jeweler’s rouge on a felt wheel with my high speed
rotary tool running at the slowest speed to final polish the
butt plate. I took
the counter sink bit and cut away the excess epoxy from the
screw hole. As
shown in the above photo, you can see the epoxy patch, but the
shape is now nice and smooth.
I was actually very surprised how well this repair
turned out. I had
thought about applying a coat of paint, but I decided not to
because I felt the paint might flake off over time, and I
wanted to show-off my repair.
Result
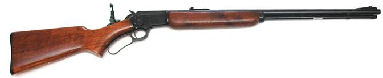
The
photo above shows the result of my work.
The wood actually came out a little lighter in color
from the original, but you can see the semi-gloss finish from
the Tru-Oil®.
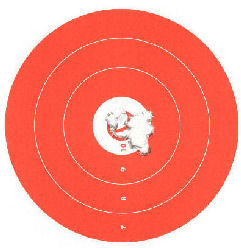
The
real question is, however, how does it shoot?
Well, this is one sweet rifle to shoot, and I can see
why it is so popular and still in production.
The action is smooth, the trigger is light and crisp,
and it pretty much shoots into one hole. The above
target is 15 shots at 25 yards.
Overall I’m not only pleased with my work, but I’m
very pleased with the rifle.
I’ll be shooting this one for many years.
|